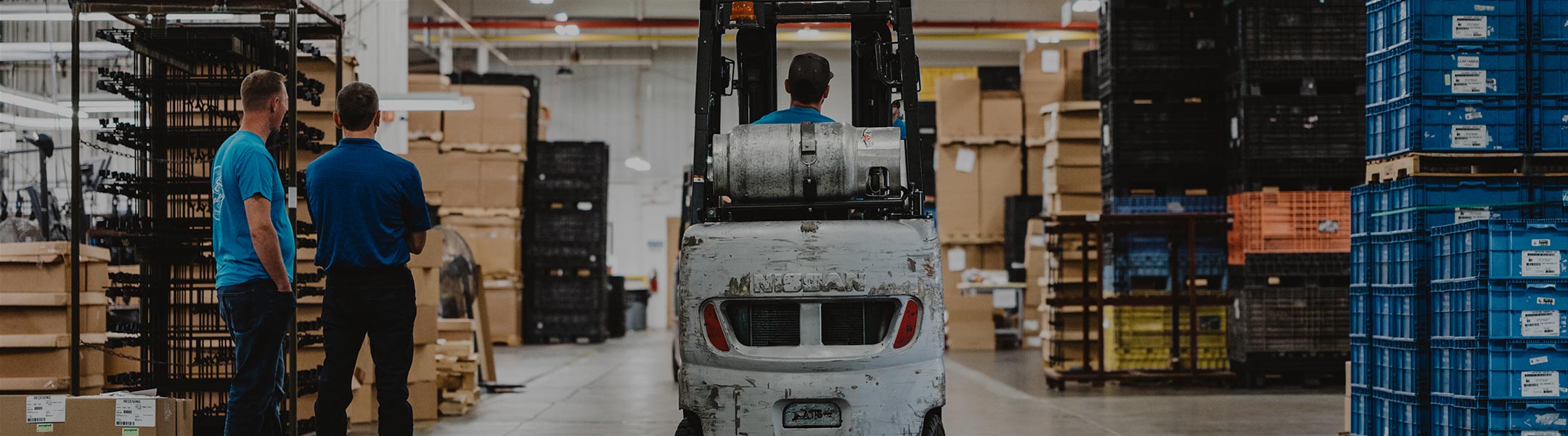
Get your copy of the 7th Annual State of Smart Manufacturing and hear from 300+ manufacturers in this new survey report!
For a monthly digest of expert insights, data points, and tips like the ones in this article.
Global manufacturing is increasing in complexity as new challenges arise, customer expectations change, and best practices evolve. This complexity makes it more challenging than ever to manage a production floor effectively.
With traditional manual tracking, this process is inefficient and costly. Today, most companies turn to technology in the form of Manufacturing Execution Systems (MES) to help manage and control their floor.
An MES allows monitoring, tracking, documentation, and control of the entire production process. It’s intimately linked to production but extends through integration with ERP systems and other software to impact quality, inventory, planning, and more.
A properly configured MES gives teams complete visibility and control over production processes at near real-time speed. This capability enables continuous improvement, advanced quality and maintenance strategies, and process optimization.
When data collection is automated and analyzed in a cloud-based platform, data becomes an even more significant asset to managing an operation. The extensibility of an MES through upstream and downstream variables delivers insights and value through KPIs accessible across the enterprise.
Benefits of MES KPIs include:
Manufacturing teams, from operators to managers, need context to understand their immediate and long-term challenges. KPIs inform them of what’s happening across the floor and what needs to be addressed immediately.
KPIs also help predict the current reality's outcome and what long-term trends and performance can be expected. These predictions help teams develop strategies and plan for labor, capacity, and other variables.
Here are a few of the critical KPIs an MES should use to inform and predict:
Long considered the holy grail of production, reducing downtime is always on the minds of those in manufacturing. An MES should allow operators and managers to see real-time downtime across various views such as spindle, machine, operator, shift, machine grouping, or plant.
With an MES as part of a smart manufacturing platform, downtime KPIs enable intervention, planning, and decision-making.
While all machine setup time is downtime, not all downtime is due to machine setup. A KPI that tracks machine setup provides valuable information to help teams develop strategies to reduce setup and "on spec" time.
Staging setup teams and other innovative strategies can be used to reduce this category, improving uptime and startup quality.
First-pass yields filter out rework and scrapped parts so that only first quality is counted. Because an automated, cloud-based MES is extensible across a wide range of inputs, sensors, optical scanners, and readers may be added to the system to improve this KPI.
Beyond first pass yields, teams learn the reasons for the off-quality and further dig into problems using KPIs for scrap and rework quantities.
OEE is a function of three measured variables: availability, performance, and quality. An OEE score will help teams develop process improvements that lead to higher productivity and efficiency by multiplying these factors.
An MES system will also be able to break each of the three factors into separate KPIs for more granular improvement techniques.
Capacity utilization reflects how efficient and productive resources are for a given machine, department, shift, or facility. Different KPIs may be used for production capacity and labor capacity for better resource planning.
Many manufacturing companies operate with perishable inventories or regulatory restrictions placed on their use date. Others utilize factoring to manage cash flow against aged inventory.
An MES should provide a KPI for managing the "turns" of the inventory. This figure helps teams plan purchases, manage cash in the finance department, plan and schedule production, and more.
Let's face it; customers are less likely to reorder if products aren't delivered on time. A cloud-based MES should reach far back into the supply chain to ensure the most efficient production. It should also reach forward and gauge the success of the production efforts.
With service-level KPIs for on-time delivery, returns, and other areas, planning can be improved and production strategies sharpened to guarantee finished goods are delivered on time and with the fewest defects.
Looking for the right MES that can provide accurate, actionable, and real-time data? Plex offers the industry’s best MES solution that covers the above KPIs and many more. This software integrates with other systems, such as MRP and ERP software, to bring the power smart manufacturing and connected insights to the entire enterprise.
Discover market trends and learn why Gartner named Plex a leader in the 2022 Magic Quadrant Report for MES.