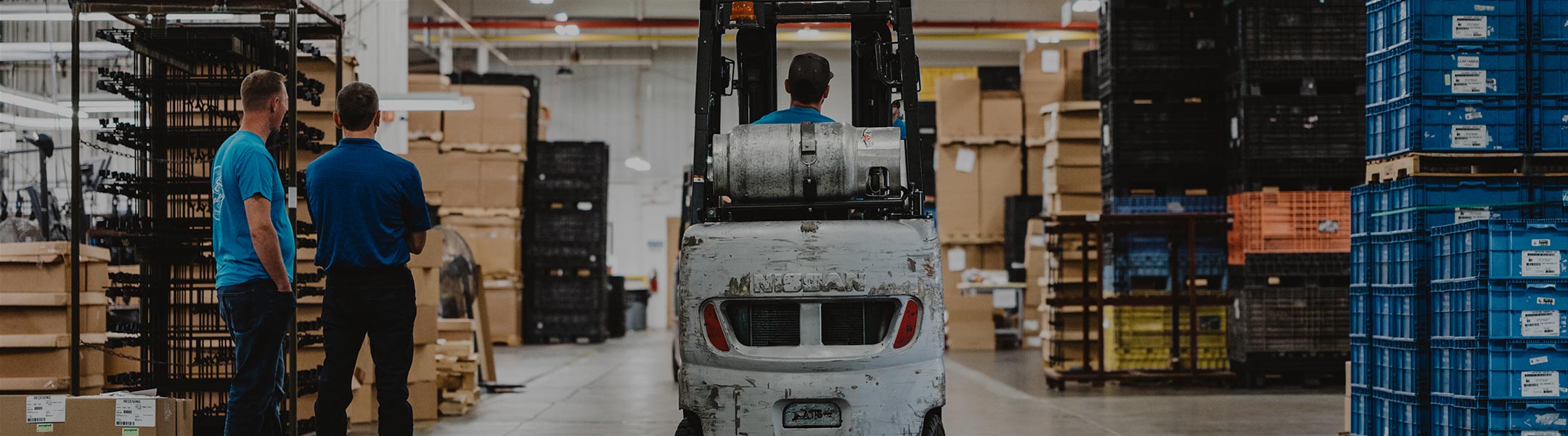
Get your copy of the 7th Annual State of Smart Manufacturing and hear from 300+ manufacturers in this new survey report!
For a monthly digest of expert insights, data points, and tips like the ones in this article.
The Industrial Internet of Things (IIoT) is a technology trend that manages to be overhyped and underrated at the same time. On one hand, IIoT is overhyped because for every optimistic projection about how much of the typical production line will be automated and robotized 10 years from now, according to some experts there’s the reality that fewer than 14 percent of the machines on shop floors are currently “connected.”
On the other hand, IIoT can be considered wildly underrated and under-applied. Because relatively few companies have pursued IIoT implementations in earnest, whatever results they’re reporting only scratch the surface of what’s possible.
Here’s how to interpret the hype, and how IIoT fits in within the broader Industry 4.0 movement.
The IIoT “hype” would have you believe that to fully realize the value of IIoT, manufacturers that want to increase their efficiency must immediately and additionally invest in technologies such as machine learning, augmented reality, and artificial intelligence.
This isn’t true.
A much wiser and more pragmatic approach is to focus on your most critical business needs and then implement and apply the technologies that will best address these needs.
Here are some of the biggest problems today’s manufacturers face:
To address these and other challenges, you need not chase after every cutting-edge technology available on the market. When we speak with clients we hear “we know that there are great benefits in using IIoT, we just don’t know where to start or how to articulate the benefits or ROI.” Too often, IIoT projects start with a focus on the sensors and data collection rather than what business problem needs to be addressed.
Once you know what problem you are solving and how you will measure the benefits, the next step is to create a pilot to validate your business case on ROI.
Too many people talk about deploying IIoT as if it’s a discrete project – something you do once, and then move on. This is hype.
IIoT is a multi-phased journey that offers higher dividends as time goes on, and the best way to start your IIoT journey is with a small project that can generate immediate business value. Once you have an IIoT foothold, it’s easy to scale up and start addressing the pain points in your business, such as identifying bottlenecks in production, reducing waste, or optimizing the supply chain.
Our customers tell us they don’t see IIoT as a major expense that will only yield results far off in the future—they see it as a practical investment to do more with the technology they already have.
Consider MPI Corporation, a group of companies based in Indiana that provides metal fabrication and distribution, which applied Industrial IoT to a clear business case. “Based on what we've seen of ROI so far, we expect a 30% reduction in unplanned downtime cost, about a 10% reduction of plant maintenance, about a 10% reduction in job transition time.”
By implementing IIoT technology little by little, you can gain more visibility into your existing assets and start planning your strategy for making major improvements in your operations. Yes, this strategy may someday incorporate cutting-edge technologies such as AI and machine learning. But the important thing is to get started now with the technologies that can help you make incremental improvements to your bottom line. Don’t miss this opportunity to maximize your efficiency and safeguard your profitability.
Download the eBook “Make The IIoT And Digital Transformation A Reality” to start your planning and evaluation process today.