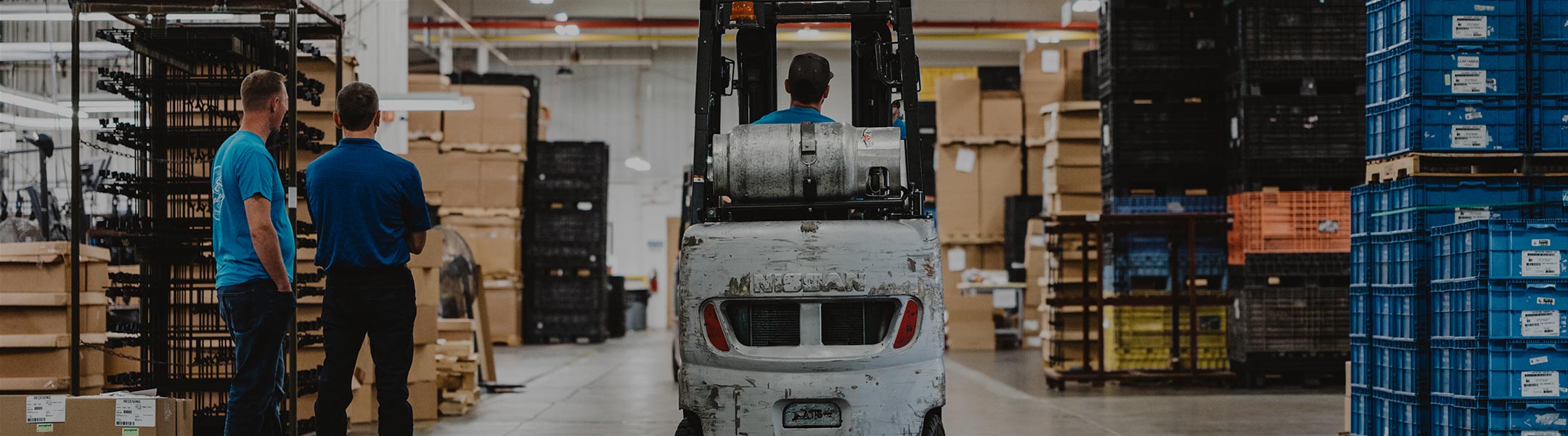
Get your copy of the 7th Annual State of Smart Manufacturing and hear from 300+ manufacturers in this new survey report!
For a monthly digest of expert insights, data points, and tips like the ones in this article.
“This year automakers have recalled more than 48 million vehicles in the United States, surpassing the previous record of about 30 million in 2004.” New York Times, 9/14/2014
“According to the Original Equipment Suppliers Association (OESA), warranty claims reported by publicly traded companies range from $11 billion to $13 billion a year. That’s a powerful incentive for automakers to hold suppliers liable, and they generally find ways to do so.” Automotive News, 10/27/2013
All the recent news about recalls in the motor vehicle industry got me thinking about quality management. In 1979 I was the VP of Manufacturing in a company producing switches and motors for the appliance industry. That was the year that Philip Crosby published his best-selling book, “Quality Is Free” and it set off furious debates in my company and throughout manufacturing. Those of us who actually read Crosby’s book, rather than scoffing at it, realized that what he was really pointing out was the extremely high cost of poor quality or as he would have said – “nonconformance.”
There was a prevailing view in manufacturing in those days that while quality was desirable it had to be balanced against productivity and cost. We used to say, “Time, cost, quality? Pick any two…”. This idea that there is a zero sum game where any increase in quality must result in higher costs or lower productivity was what Crosby attacked with a vengeance. Unfortunately as I read about some of the quality problems in today’s manufacturing companies it appears that there may be a new generation of leaders who haven’t learned the lesson that great quality increases throughput and lowers costs, as I’ll discuss later on.
The motor vehicle industry often gets singled out for its quality issues with endless headlines and news stories about massive recalls. The reality is that there is probably no manufacturing segment that has worked harder to improve its product quality and most of the really important quality management concepts and techniques were developed or perfected in the auto industry. The problem is that cars and light trucks are incredibly complex “systems” with something like 30,000 parts each and in North America we produce more than 16 million of them per year. That’s a lot of opportunity for defects!
Philip Crosby came along well after the Total Quality Management (TQM) pioneers like Deming, Juran, and Ishikawa but he made two really important contributions to the subject. He emphasized the extraordinarily high (and often hidden) costs of poor quality and he was convinced that the solution to the problem was prevention. The auto industry, with its incredible high velocity supply chain, is a perfect example of both:
Start with a metal stamping company that is producing 5,000 hinge brackets per day but on one of those days a material handler delivers the wrong steel strip to the press. It looks like the right stuff but it is way too hard. The brackets get stamped and that night they are delivered directly to the production line of a Tier One seating manufacturer. Within two days those brackets have been assembled inside seating systems that are now sequenced and are on their way to an auto assembly plant. Hours later they roll off the end of the line and are headed to dozens of dealerships across the country. In a matter of a few weeks those defective brackets are in some consumer’s shiny new car. A few months later that consumer gets in a collision and the seat back snaps at the hinge. There are lawsuits, investigations, an NTSB inquiry and finally it’s determined that the hinge bracket was too brittle.
Here’s where the cost of poor quality starts to mount up. The OEM faces massive legal expenses and a multi-million dollar settlement. The dealer, the OEM, and the seating manufacturer have all had major damage done to their reputations. After endless litigation the costs will be shared across the supply chain and ultimately the poor metal stamping guy will lose his best contract and may very well lose his business. All this happened because of one wrong coil of steel.
As Crosby says the only way to avoid this all too common scenario is prevention. The car manufacturer couldn’t inspect the brackets because they were already inside the seats. The seat manufacturer might have tested some of the incoming brackets but most of the ones in the container were made with the right material. The only way to truly “prevent” this from happening was to have a system in place that forced the press operator to scan the coil before loading it on the machine. That scan would have shown that it was the wrong material and the only cost would have been the time to go back to the warehouse for the right lot. Imagine what this company could have done with the time and money wasted on that recall.
Quality really can be free!
The real key to great quality is recognition by management that poor quality is very, very expensive and modern technology has made prevention much easier and more effective.