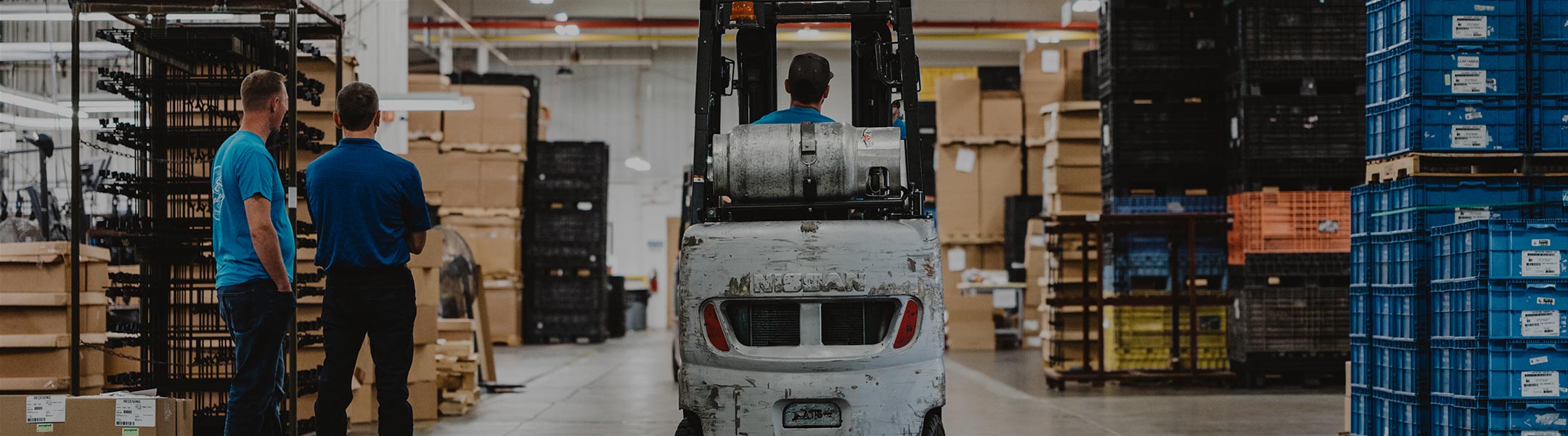
Get your copy of the 7th Annual State of Smart Manufacturing and hear from 300+ manufacturers in this new survey report!
For a monthly digest of expert insights, data points, and tips like the ones in this article.
“Automation” means different things to different manufacturers, depending on the equipment, systems, and processes in place. But many companies only automate some of their processes, leaving others disconnected or with manual processes still in place.
Part of the explanation lies in the equipment that manufacturers use. Having purchased OEM equipment with partial or complete automation, they simply use it for machine-specific data, even printing thermal printouts to add to spreadsheets manually. The equipment is never connected to other systems or enterprise-level software like an ERP.
There’s also a tendency for companies to use multiple software platforms that aren’t connected either. This software may help one department, but the lack of interoperability means that the silos of data have been digitized with no benefit outside the area where the software was established.
True automation is only realized when all machine assets and software systems are united in a single version of truth under one standardized umbrella. When this happens, data is cleansed and organized for consumption by cloud-based analytics.
There are many benefits to process automation under a single smart manufacturing platform, including:
To realize the full power of the benefits above, the first step is to get connected. Connecting your plant’s equipment, sensors, and monitoring systems to the edge allows you to control the flow of information throughout your processes.
Once connected, you can automate countless manual tasks across the factory floor. This automation will increase speed and production efficiency, improve safety, and reduce operator and data entry errors.
Once your processes are automated, you can track all production and quality at multiple levels, such as by operator, machine, spindle, and more. As this automation reveals new trends, decision makers can act quickly to head off problems and improve processes.
Beyond process automation, advanced analytics takes your automation even higher. Workflows can be updated automatically as changes are made. And depending on equipment type, many decisions can be autonomous or semi-autonomous.
With the Plex Smart Manufacturing Platform, there’s no need to rely on partial process automation with fragmented systems that don’t communicate. By leveraging a fully connected data platform, the complexity and cost associated with automation systems have given way to flexible, agile software that drives process automation throughout a factory.
It’s not only cost-effective; it uses the power of real-time data to generate value well above adoption cost to optimize your processes through complete automation. Plex puts your data to work to further automation in your MES, ERP, and other company processes and take your production to the next level.
To learn more about automation in the industry, download the Automation Edition of the 7th Annual State of Smart Manufacturing Report.