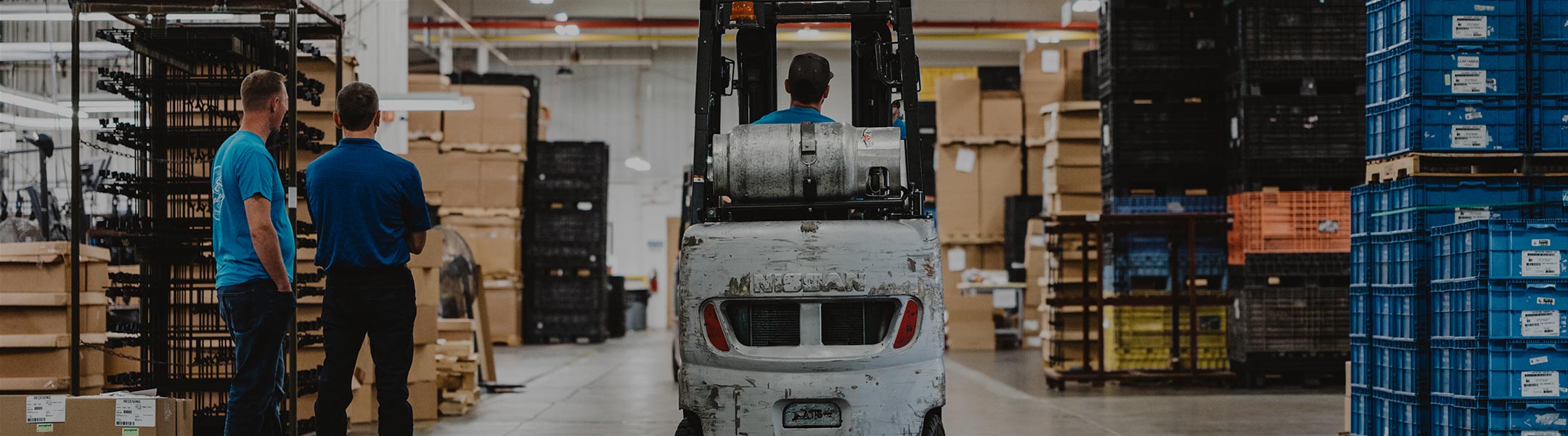
Get your copy of the 7th Annual State of Smart Manufacturing and hear from 300+ manufacturers in this new survey report!
For a monthly digest of expert insights, data points, and tips like the ones in this article.
Today, digitization across most industries is driving the next industrial revolution in manufacturing. As companies and OEMs seek to build digital capabilities within their production systems, smart manufacturing becomes standard for anyone looking to get ahead.
This trend is most often explained in terms of data and advanced analytics as a path to improved quality, process optimization, and a host of other benefits. But when undertaking the digitization journey, what do you do with that data? And how do you ensure that it makes sense to the analytics engine meant to deliver actionable insights?
While accurate data is good, accurate real-time data is even better. However, raw data alone needs context to be valuable and without it, analytics may render faulty or misleading information. These insights could lead to misinterpretations that result in flawed decisions.
So, what is contextualized data? Contextualization means moving beyond traditional data utilization to apply additional information relevant to the process or operation. This information can be as simple as time stamps, location, or source.
In smart manufacturing systems, even operator-added data could be included to increase data importance and provide background for an operation. These elements allow interoperability across systems so that MES, QMS, ERP, SCP, and other programs work with real-time information.
The first step in unlocking smart manufacturing’s impact through contextualization is to digitize your operation. Data importance in modern manufacturing cannot be overstated, and connecting physical assets in infrastructure to collect, cleanse, store, and analyze that data is critical.
Different functional areas - like production, quality, maintenance, and engineering - need different types of information to perform their tasks.
Traditional systems using manual data collection were siloed and delivered in weekly or monthly reports. But manufacturing is complex, and without digitizing an enterprise, data will be limited in its capabilities. Digitization requires a strong data strategy and implementation plan alongside a commitment to building out a system of connected assets.
In a digitized production system, data utilization becomes more about adding industry-specific context to turn the raw data into usable information for analysis.
Contextualized data can include:
Companies like yours can only unlock access to smarter manufacturing capabilities with complete digitization and contextualized data. Analytics and tools such as machine learning can be powerful allies for improvement. However, with fully contextualized data, the analysis is more precise and more likely to render actionable insights that truly improve performance.
Contextualized data also benefits different functional areas within manufacturing. Formerly siloed systems now utilize the same data in context to how it applies to their mission. This improves communication and ensures that functional areas like production, maintenance, engineering, QA, and others are in sync and not working at cross purposes.
The journey to smart manufacturing is not a switch or a magic pill. It requires a sound data strategy and implementation of digital technology. Once that decision is made, it’s critical to contextualize data to let the new infrastructure work at its full potential.
Discover more smart manufacturing trends and tips for putting your data to work in our latest State of Smart Manufacturing Report.