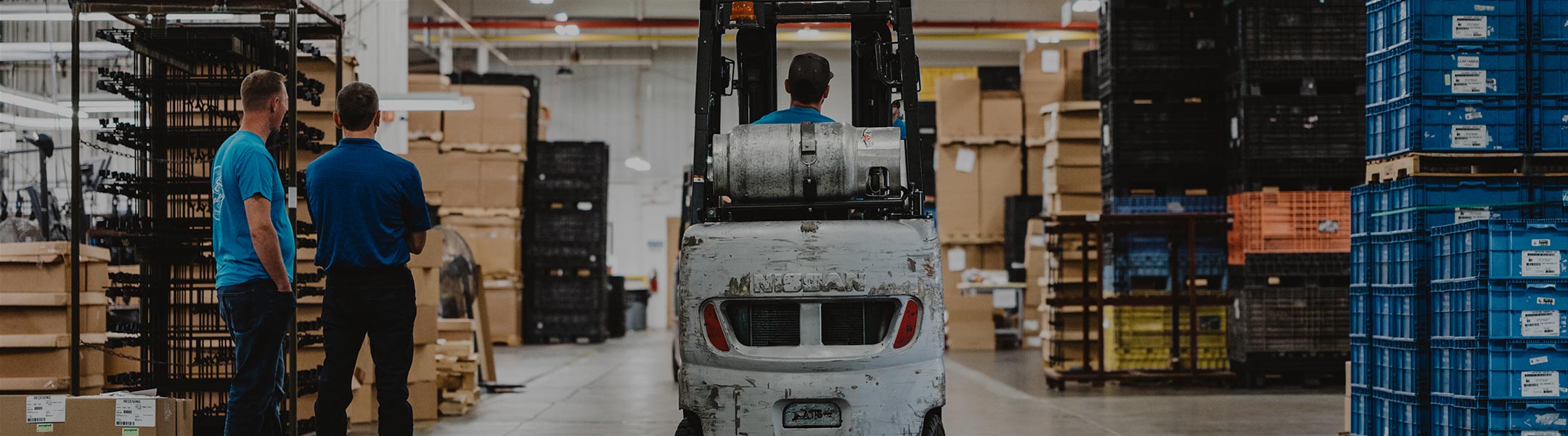
Get your copy of the 7th Annual State of Smart Manufacturing and hear from 300+ manufacturers in this new survey report!
For a monthly digest of expert insights, data points, and tips like the ones in this article.
I had an interesting conversation last week with a company that was evaluating new ERP systems. One of the principal drivers for replacing their old business system is compliance and traceability. Today they use a combination of manual processes and disconnected systems to track material usage, quality, and production activities. If there were a problem that necessitated a product recall or a lot or serial number trace, they know they would be in big trouble. At the moment they don’t have a government-mandated compliance requirement, but they worry about potential litigation issues and their customers are beginning to demand better and faster traceability capabilities.
They assured me that all of the solutions they were evaluating had strong compliance capabilities, including the ability to produce lot and serial number genealogies directly from the ERP system. However, when I asked them if any of the systems they had looked at were capable of “active compliance,” there was a long pause and I realized that they had no idea what I meant. Most modern ERP systems offer “passive compliance,” which means that they record transactional information about material lots from the point of receiving, through production, and on to shipping. They maintain an audit trail that can be queried from the raw material lot forward or the customer order backward. For many companies this represents a huge improvement over their current state but it really isn’t adequate. This approach doesn’t help prevent problems—it only helps find them after they have occurred.
The Plex Manufacturing Cloud is uniquely designed to provide active compliance. We can certainly produce traceability reports but our focus is making sure that the problems never occur in the first place. The Plex system is monitoring and controlling activities in real time, so it won’t let an operator start a job if the wrong material or lot were delivered to the workstation. It makes sure that the employee is properly certified to run the equipment. It displays text or video work instructions to ensure that the right steps are followed. It enforces any required tests or inspections, monitors the calibration of the test equipment, and stops the job if the process goes outside the control limits. In most cases the information is captured directly from the equipment, so the data is accurate and there is no impact on operator productivity.
The problem with passive compliance is that it only looks backward. At Plex, we understand that given the pace of today’s manufacturing environment, anything less than real-time compliance is just too late. If you make the wrong parts or batch in the morning, it could be used in end products by afternoon and shipped to your best customer that evening. At a minimum you have created a scrap or rework nightmare, but you may have a much more significant customer satisfaction or product liability problem. An ERP system helping you reconstruct the history will not make up for the damage that was already done.
Active compliance requires a combination of functional depth and integration that other ERP systems simply don’t have. At the moment that an operation is about to begin, the system must have access to the employee training certifications, the material and lot data, the process routings and work instructions, the quality check sheet requirements, and a host of other information. Individual companies or vendors might try to assemble this capability from a variety of separate systems but the result is an environment that is expensive, complex, fragile, and difficult to use. It can take months or years to build the integration and every time the process or the one of software pieces changes, it sets off another IT development and testing project.
If your ERP system is really going to prevent bad things from happening, everybody on the plant floor has to be connected to an integrated system. Receiving clerks, material handlers, machine operators, quality personnel, and supervisors all have to interact with the same information. This simply can’t be done with a “portfolio” of applications even if the same vendor owns them all. It requires a single database, single architecture, single user interface, and functionality that stretch from Finance and HR in the back office to quality management and machine automation on the plant floor.
As you think about your next generation ERP system, there is bound to be lots of discussion about compliance and traceability requirements. I would suggest that you need to consider whether you want to settle for the passive approach to auditing and reporting or if this is the time to step up to an active compliance environment that can both reduce liabilities and improve productivity.