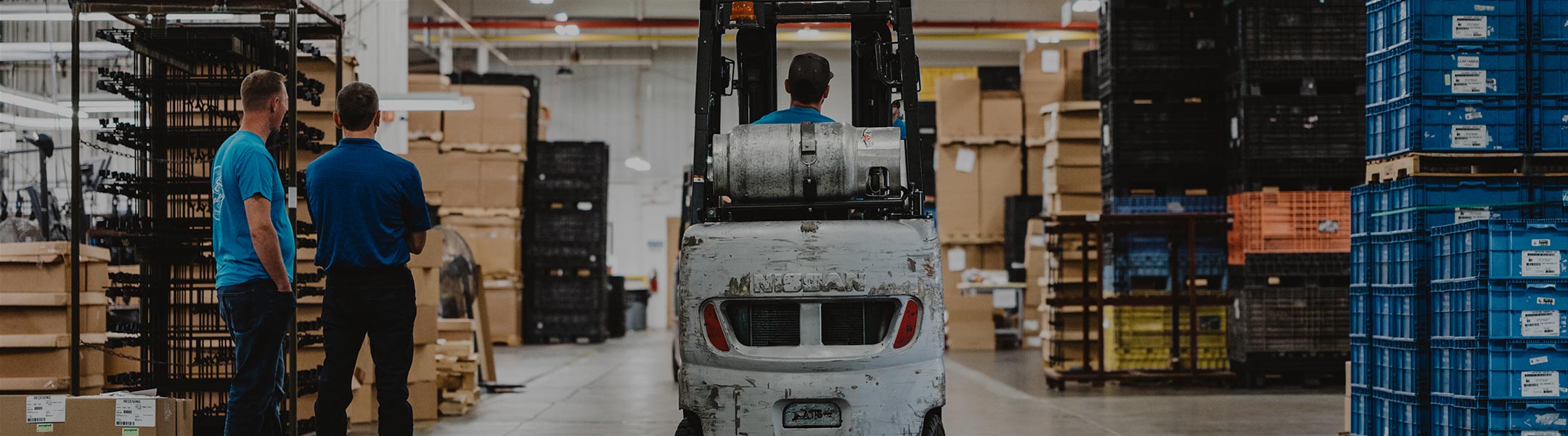
Get your copy of the 7th Annual State of Smart Manufacturing and hear from 300+ manufacturers in this new survey report!
For a monthly digest of expert insights, data points, and tips like the ones in this article.
Inventory traceability and tracking is all about creating a paper trail of inventory that reflects physical reality. Many companies manually record inventory basics like shipping receipts for raw materials, warehousing, issues from stock to production, and shipments of finished goods to customers. This may work when your company is small but when your company grows or customer demands become more complex, manual or paper-based recording creates timing problems and accuracy concerns. Without a rigorous digital system, it is too easy for people to move material without documenting resulting in scurrying around the facility to find missing inventory. Confusion and delays increase the likelihood of stock-outs and result in the need to purchase excess inventory to account for all of this uncertainty.
Here are seven inventory tracking and reporting best practices that can improve inventory accuracy and reduce excess inventory and the associated carrying costs:
1. Receiving
Barcode label everything that comes in the door to start your traceability tree. Provide your suppliers with your label formats so parts are already identified as appropriate for your system when they arrive. Documenting the supplier the shipment came from give you “one back” in your traceability tree.
2. Movement
Scan everything that moves. It’s good to know what you have on-hand. It’s even better to know precisely where it is.
3. Locations
Scan to track movement to and from locations that are clearly defined in your facility(s). It is absolutely critical to have a disciplined location identification scheme with each location tagged for scanning.
4. Work in Process (WIP)
Scan every WIP move, such as when loading all material to each line or work center. Tracking movement between work areas can help reduce the excess inventory needed to cover material uncertainties stemming from no visibility into WIP.
5. Inspection
Add a scanning step to each quality inspection to add traceability. Scan receipts into an inspection area or work center. Scan release stock, return to supplier, reject, or rework to ensure timely updates and correct identification and tracking. For process manufacturers especially, inventory traceability is key to quality management for recalls and isolating the scope of a recall.
6. Outside services
Scan “out to” and “in from” outside organizations. If outside processing contributes significantly to your lead times, be sure to track when jobs go out and come back from service providers. Additional process control can be achieved with bin-for-bin tracking while at the outside facility.
7. Shipping
Label each shipping container, and scan every item that goes into a container to provide an accurate accounting of its contents. While this is standard practice for most manufacturers, those implementing end-to-end labeling and scanning from receipt to shipping typically experience greater tracking accuracy. Including the “ship to” information adds the “one forward” to complete the traceability tree.
Want to get an even deeper look at effective inventory control? Download the white paper: Taking Control: Improved Inventory Visibility Leads to Lean Success.